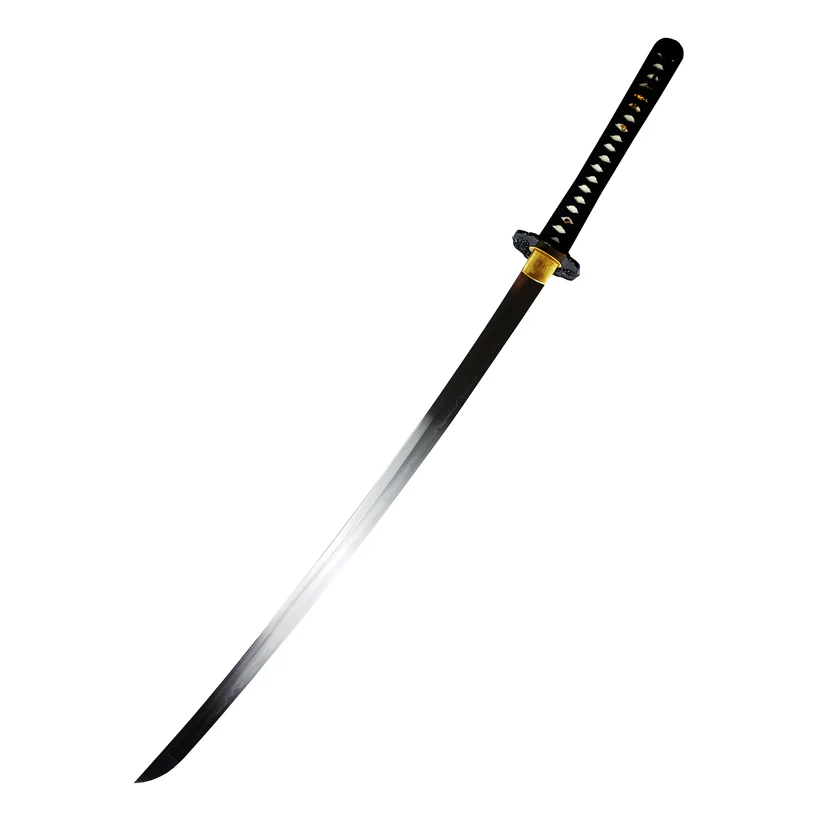
The Different Katana Steel Types Explained for Buyers
Share
Modern katanas use several types of steel, from basic carbon steel like 1045/1060 to high-end tool steel like T10. The old-style steel called tamahagane has 1-1.5% carbon and shows clear folded layers. Some blades are heated to be equally hard throughout, reaching hardness levels in the low 50s HRC. Others are heated differently in various parts, making the edges much harder at 58-60 HRC. Steels that work like springs, such as 5160, bend well and stay strong, while steels with lots of carbon keep their sharp edge longer. Knowing these differences helps buyers pick real, working swords.
Key Takeaways
- 1045 steel offers an affordable entry point for beginners, while 1060/1095 carbon steels provide better performance for serious practitioners.
- Spring steels like 5160 balance flexibility and strength, making them ideal for cutting practice and martial arts training.
- Traditional tamahagane steel features distinct layering and hamon patterns but costs significantly more than modern production steels.
- Differentially hardened blades offer superior edge retention and shock absorption compared to through-tempered alternatives.
- Avoid stainless steel katanas for practical use, as the high chromium content makes them unsuitable for cutting applications.
Understanding Traditional Tamahagane Steel
Tamahagane steel is one of Japan’s most important metal-making breakthroughs. Made from iron sand in special furnaces called tatara, this steel contains just the right amount of carbon - between 1-1.5% - which helps it stay sharp and cut well.
The steel goes through a long process of heating and hammering over and over, building up many layers that make it strong yet bendy. Craftsmen use special heating methods to create blades with both hard and soft parts. This careful heat treatment gives the blade a tough body and a very sharp edge.
You can see the skill of the maker in the beautiful patterns on the blade, especially the wavy hamon line that shows how the steel was heated.
These features, along with the steel’s special mix of natural elements, make Tamahagane a perfect example of old-world metal-making at its best.
Modern High-Carbon Steel Options
Today’s katana makers use different types of strong steel that mix old-world skills with new metal science.
The basic choice is 1045 carbon steel, which is strong enough and costs less than $100. Better than that is 1060 carbon steel, which stays sharp longer and is tougher, costing between $150 and $500.
For the best quality, makers use 1095 carbon steel, which holds its edge very well and is extra hard, but needs careful heating to keep it from breaking.
These swords usually cost $200 to $600. Another choice is spring steel, mainly type 5160, which bends well without breaking.
At about $250, 5160 spring steel sits in the middle price range and gives both strength and flexibility, making it a top pick for many modern sword makers.
Through-Tempered Vs Differential Hardening
Heat treatment shapes how a katana performs, with two main methods used today: through-tempering and differential hardening. The old Japanese way of differential hardening makes blades that are harder in some parts than others, creating the wavy hamon pattern and balancing sharp cutting with strength. Through-tempered steel blades are the same hardness all the way through but trade a sharp edge for overall toughness.
Characteristic |
DH Katana |
TH Katana |
Edge Hardness |
58-60 HRC |
Low 50s HRC |
Spine Hardness |
38-40 HRC |
Low 50s HRC |
Edge Retention |
Superior |
Moderate |
Shock Absorption |
Excellent |
Good |
Polishing Ease |
Complex |
Simple |
These different hardness levels affect how the swords work. Differentially hardened blades keep their edge better and handle impacts well, showing why Japanese sword makers chose this method for their craft.
Folded Steel Construction Methods
Folded steel construction is a time-tested method where skilled makers heat, hammer, and fold steel over and over to build up many tiny layers in the blade.
In the past, this folding helped remove dirt and made Japanese swords stronger, but today’s steel-making is so good that all this folding isn’t needed anymore.
Modern makers should be careful not to fold the steel more than 16 times, as this can weaken the blade instead of making it better. The main reason people still use this method is to create beautiful patterns that show how the blade was made.
When done right, folded steel makes hard, good-looking blades, but poor technique can make them too brittle and break easily.
Common Steel Types in Production Katanas
Production katanas are made with different types of steel, each bringing its own benefits to sword making.
Basic steels like 1060 and 1095 become very hard and keep their sharpness well when heated the right way, which is why many good swords use them.
Spring steels, mainly 5160 and 9260, bend without breaking and stay strong, which helps when the sword hits things hard.
Tool steels like T10 and L6 are top-grade choices that last longer than regular steel types.
While some decorative swords use stainless steel, it contains too much chromium and isn’t strong enough for real sword use.
Cheaper production katanas often use 1045 steel, which works but might not be very good quality.
Identifying Quality Steel in Katanas
When looking for a good katana, you need to know what makes the steel high-quality. The best katanas use high-carbon steel, mainly types 1060 and 1095, while spring steel works great for fighting practice.
One clear sign of quality is a real hamon - the wavy line on the blade that shows it was properly heated and cooled.
Good katanas come with papers that show how the steel was heated and what type of steel was used. While cheaper steel like 1045 can work okay, serious users should pick blades with more carbon.
How well the blade holds its edge and bends without breaking depends on both the steel type and how it was heated, so these two things matter most when checking quality.
Price Points for Different Steel Grades
The price of a katana depends on the steel used to make it. Basic katanas made with 1045 carbon steel cost less than $100, while stronger 1060 carbon steel swords sell for $150-500.
High-quality 1095 carbon steel katanas, known for keeping their sharp edge longer, cost between $200-600.
Spring steel katanas offer special features. The 5160 steel swords cost around $250 and are both strong and bendy.
The 9260 steel, which handles impacts well, sells for more than $200.
The most expensive katanas use tool steels like T10 and L6 Bainite. These top-end swords are very hard and stay sharp for a long time, making them popular with serious collectors and martial artists.
Maintenance Requirements by Steel Type
Different types of steel need different kinds of care to stay in good shape and keep working well.
Each type needs its own way of care to work best and last longest.
- High-carbon steel katanas need regular oil to stop rust and keep the blade strong.
- Stainless steel needs little care but should be cleaned to stay bright.
- Spring steel blades work better with wax to stay bendy and keep water away.
- Tool steel swords need cleaning and oiling after use to stay sharp.
- Layered blades need careful watching to keep water from hurting the layers.
Sword owners must know these care needs since good care helps the blade last longer and cut better.
Looking at the blade often and cleaning it the right way helps stop rust while keeping what makes each steel special.
Frequently Asked Questions
What Type of Steel Is Best for Katanas?
The best katanas are made from steels with lots of carbon, such as 1060 and 1095. When heated and cooled correctly, these steels stay sharp longer and resist breaking. Spring steels also work well because they can bend without snapping during use.
Which Is Better, 1060 or 1095 Carbon Steel Katana?
The two steels each have their own strong points. 1060 steel is tougher and less likely to break, while 1095 steel stays sharp longer. What matters most is how well the blade is heated and cooled during the making process.
Is T10 Steel Better Than 1095?
T10 steel keeps its sharp edge longer and wears down more slowly than 1095, thanks to its special metal mix. While you can sharpen 1095 more easily, T10 has more carbon in it, making it work better for katana swords.
Which Is Better, 1045 or 1095 Carbon Steel?
1095 steel holds its sharp edge longer and stays tougher, while 1045 steel bends more easily without breaking. Which one to pick comes down to what you’re using it for. 1095 needs more careful heating during making but works better overall.
Conclusion
The selection of appropriate Katana steel requires careful consideration of both traditional and modern metallurgical factors. While authentic tamahagane remains the pinnacle of craftsmanship, contemporary high-carbon steels offer viable alternatives when properly heat-treated and constructed. Buyers must weigh factors including intended use, maintenance requirements, and budget constraints. Understanding steel properties, construction methods, and proper heat treatment processes remains crucial for making informed katana purchasing decisions. For quality Japanese swords crafted with attention to detail and authentic methods, visit Musashi Swords and explore their selection of traditionally forged blades.